Setting Shock Forces
Now it is time to discuss damping force curves. I set mine according to the suspension velocity histograms, (which I'll describe later) but roughly 65% critical damping is almost always perfect. Why? See the references below. It worked for me, and it has been independently verified by dozens of top road race teams and more than a few clued-in autocrossers.
If your shocks are set up to provide 65% critical damping over the 0-3 in/sec range, you will be very much in the ballpark - and the only way to get any better is to do suspension velocity histograms.
(One of the more rewarding things about writing this book online was seeing the reaction to this particular nugget. This, plus the natural frequency discussion on the suspension page kicked off the usual online shitstorm, but more importantly, got a whole bunch of people measuring cars, dynoing shocks, hacking Excel spreadsheets, and - amazingly enough - independently verifying this stuff. Not only is that personally very satisfying, it's a great sanity check on my work. Peer review is a Good Thing.
Some of these folks - and I'm looking at you, Scooby and Honda guys - have taken this stuff and really run with it. It's really cool to see, and makes the effort just that much more worthwhile.)
NEW 05 Jan 2011: This claim - that the ideal damping force is "65% critical over the 0-3 in/sec shock velocity range" has always bothered me. Not because it wasn't true (it is, to a couple of percent either way) but because the argument presented here has been "trust me".
For a book that has so heavily stressed that one shouldn't take anything at face value and that everything on the car needs to be tested and measured, having such an important (and dare I say it, revolutionary, based on prior setups that used insanely high shock forces) claim rest on an "argument from authority" has never sat well with me.
Happily, I have finally found some references that back me up. No more "argument from authority" and now I can sleep at night.
Racecar Engineering Magazine May 2010, "Racecar Damping" (Danny Knowlan) p.71: "when the damping ratios hit about 0.5-0.7 the car's oscillation is remarkably decreased. That's not so great at dealing with bumps, but is ideal for controlling the body when we are pitching and rolling" p.72 "In rebound from 13mm/sec to 25mm/sec [0.5 in/sec to 1 in/sec] the damping ratio is 0.7 [70%] This tells me that body control is paramount. Beyond the damping ratios blow off to 0.3. [30%] This tells me this is designed for bumps."
Racecar Engineering Magazine March 2010, "Damping - Some Food for Thought" (Danny Knowlan) p. 62 - here a picture says a thousand words:
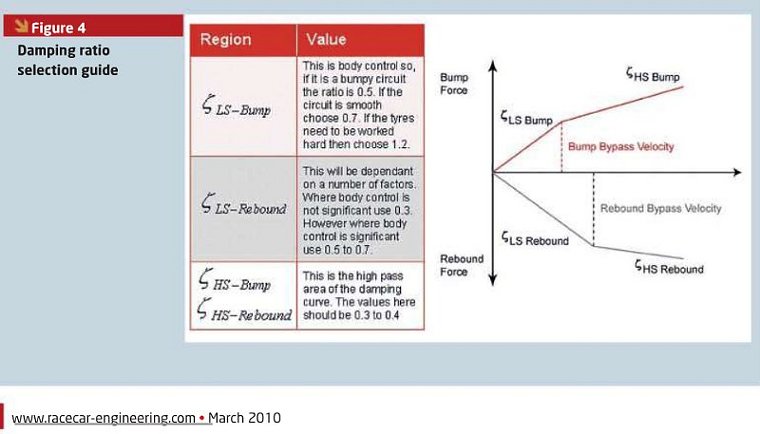
The articles go into more detail about how these numbers are calculated if you have the math for it.
I've found that people tend to run way, way, WAY too much rebound force. The usual claim is that the extra rebound increases driver feel and makes the car feel more "planted". It does - but it makes the car slower too. The suspension needs to work to work; if you lock it down with a lot of rebound you're depending on the tire alone, like a go-kart.
Again, if you are in the Stock-class game, you may not have a choice but to run tons of shock force; you are prohibited by the rules from changing springs, and stiff shocks will act like "fake springs" in transitions. But once you graduate to classes that let you change springs, shock forces should plummet.
I fell into this particular trap myself. The shocks that I won the 2002 ProSolo SM Championship on were grossly overdamped, in both compression and (especially) rebound - but the car felt great! (aside from occasionally surprise snap-spinning me into the weeds, which was the bad habit that finally forced me into rethinking my setup). When I moved to a 65% critically damped setup, the car felt way less planted; way less tied down. It was actually a little bit scary, because it moved. At turn in, the car would make a definite movement in roll to the peak roll angle, and even though that roll angle was actually pretty small, all that moving around was a little bit disconcerting. The perceived loss of grip was also completely illusionary, as the data proved over and over again that the car not only had better peak grip, but it also didn't get upset over bumps anymore. The day I crashed through one of the big Peru dips at full throttle and nearly full roll, and the car didn't even notice... wow.
Once I got used to it, the car was faster, it was easier to drive, and it eliminated a ton of bad habits from both the car and myself. As a system, we got way faster, more often, more consistently. That's a good thing!
Set the shocks at 65% critical damping between 0-3in/sec. Somewhere above that, digress the shock off to ~30% critical to handle the occasional high speed whack - the exact location of the knee in the force curve doesn't seem critical, as long as it doesn't happen during the chassis roll speed zone. And watch yourself go faster.
Setting Up a Stock-Class Car
The major limitation of a Stock-class car is that you have to run the OEM springs. That means that the proper practice of "set natural frequency with springs, damp at 65% critical" won't work.
The way I'd tackle the problem would be to adapt a strong, steel-bodied take-apart shock to the car and crank the gas pressure as high as I dared. Then I'd measure the spring force contributed by the gas pressure, calculate the revised natural frequency, and damp at 65% critical as per normal.
If that isn't an option, it is possible to "fake" a stiffer spring by going with more rebound, but there's an upper limit to how well this works. The more rebound, the slower the suspension will react, and eventually, it's effectively bound up. Furthermore, super-high rebound forces will eventually blow out seals (especially Koni yellows) so there is a durability issue as well.
My gut says that the upper limit is probably just north of critical. I have no data more solid than that. If you are knocking on 200% critical though, you almost certainly have way too much rebound.
Suspension Speed Histograms
Here's the super black magic:
Firstly, equip your car with suspension position sensors. Make sure the movement ratio of the sensor is the same as the shock, or if it isn't, calibrate the sensor until you can read the suspension position.
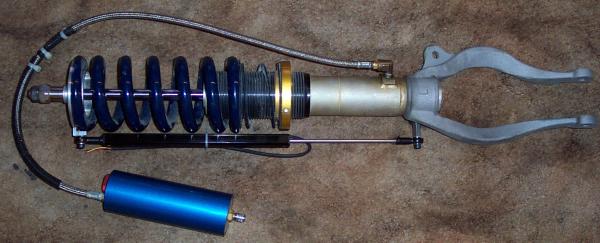
Make sure you are sampling at at least 500 Hz.
Use the math channel to take the first derivative of the position data, and now you have shock velocity data. This is worthwhile in its own right, but there's another trick coming.
Consider this: for every roll, there is an un-roll. For every bump, there is an un-bump. For every pitch, dive, heave - every chassis movement, there is an equivalent un-movement.
Which means that a histogram of shock velocities for a given shock should be symmetrical.
Which in turn means that the histograms for a given pair of shocks should be identical.
And means that the histograms front/rear should be of a similar shape, but "stretched" on the velocity axis (because of different natural frequencies front/rear they will not be identical, but they should have a similar shape).
Now you have a use for the adjuster knobs! Do a run, tweak the adjuster, do another run, and keep going until you have symmetrical, identical histograms on both wheels of the same axle, and similar shapes front to rear. What you wind up with are shocks that provide slightly different force curves, but identical reaction speeds - and you have optimised your shocks.
MOTeC's software has a wizard set up to do just this - and every major race team I know of uses this technique to tune shocks. Done on the track, done on a shaker rig... this is how it is done. And it is how I did it too.
Amazingly, 65% critical with a sharply digressive knee above 3in/sec typical Bilstein shimstack produced almost perfect histograms on my car. A little compression nudge was all they needed to become perfect. This might be blind luck, so I recommend a shock with a usable adjuster if you want to play this game. Penskes would be perfect.