Welding
No fabrication shop is complete without the ability to weld - and that means being able to weld steel and aluminum. Here is how I set up my welding bay.
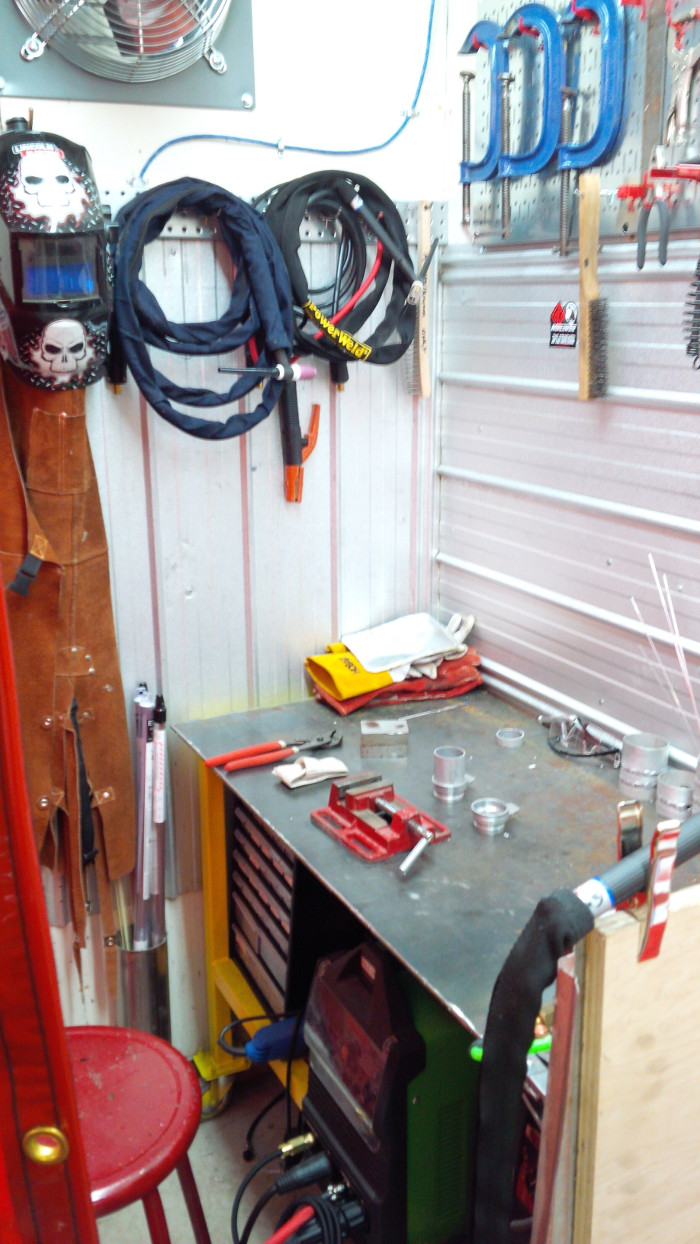
The centerpiece of any welding bay is the welding table. Happily, building a welding table is a good first project for getting into welding.
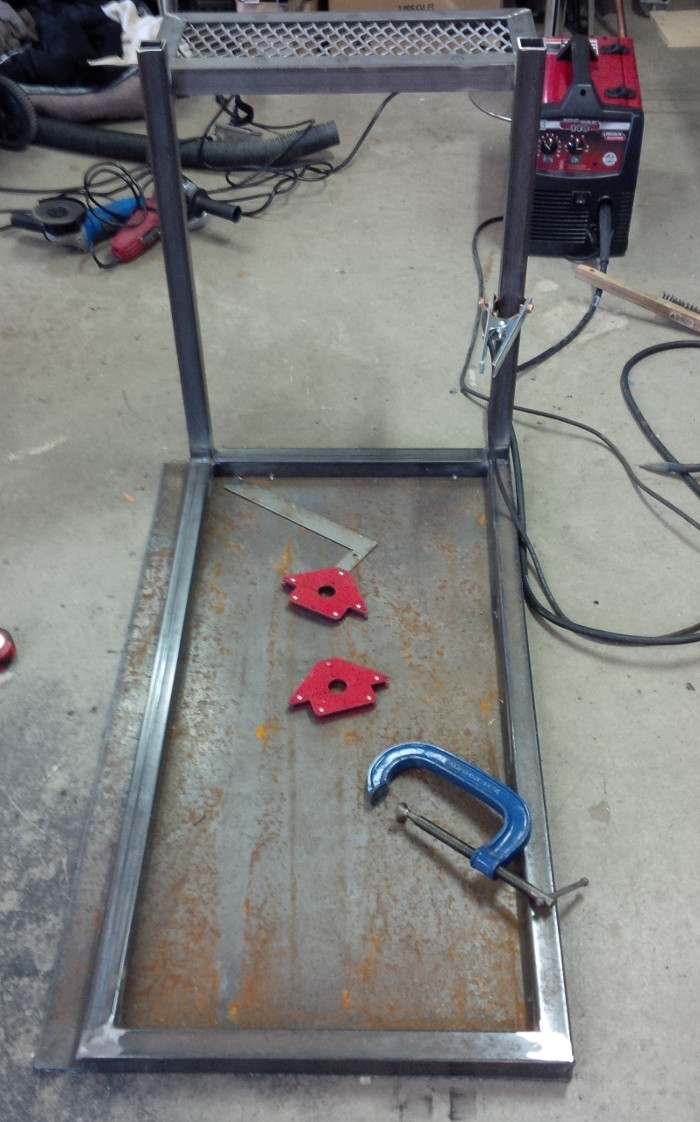
The table is all mild steel; a combination of steel plate for the top, square tube for the legs, angle iron for the shelving brackets, and expanded metal for the shelves (you want sparks to be able to drop through), all MIG welded together.
I used a Lincoln Electric 110V MIG in flux core mode to build the table. It plugs in anywhere and just hums right along. Pretty much idiot proof steel welding. The flux core is a little dirtier than using shielding gas, but that's the only downside.
Gas bottles for the MIG and TIG will go on this shelf. You wnt the bottles tied to the table so you can move it around the shop if need be.
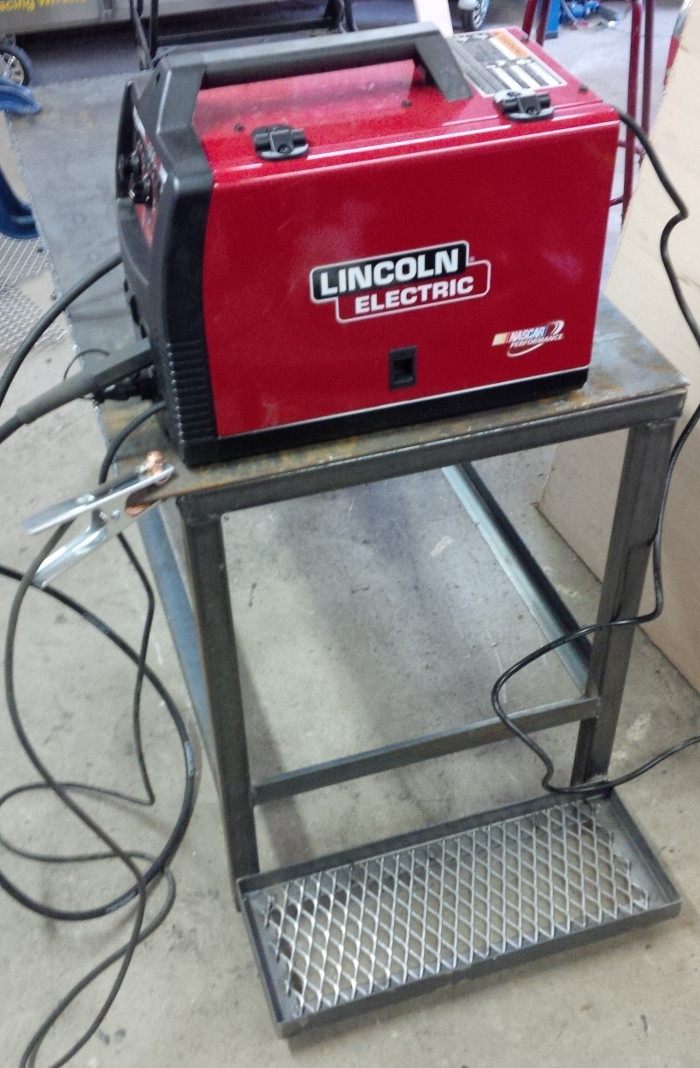
Here's what the flux core welds look like:
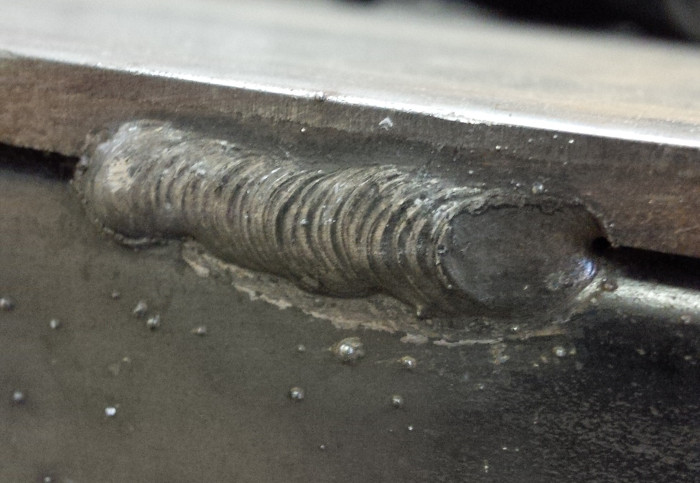
All painted up and ready for use!
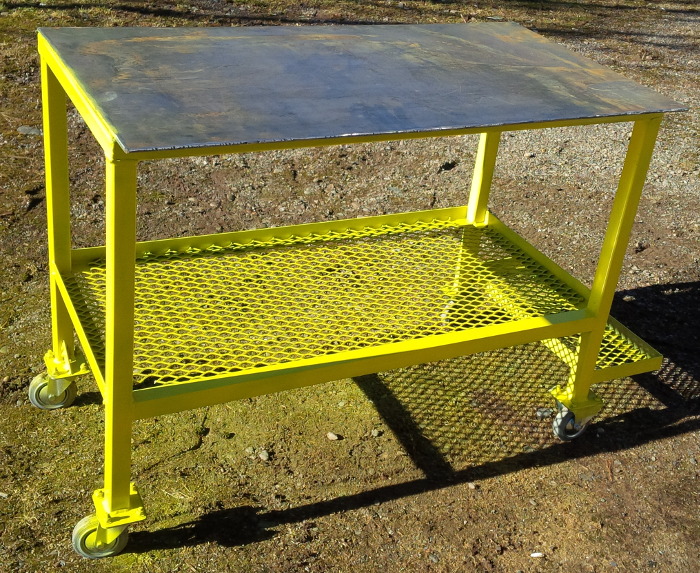
Welding aluminum needs an AC TIG welder. I wanted to buy an AlphaTIG 200DX but AlphaTIG wouldn't ship to Canada for some reason. So I got a Everlast PowerTIG 200DX instead. It is nearly feature-identical to the AlphaTIG (for more money) so I suspect a certain overlap on internal components, much the same way Chinese machine tools are constantly rebranded for North American sales.
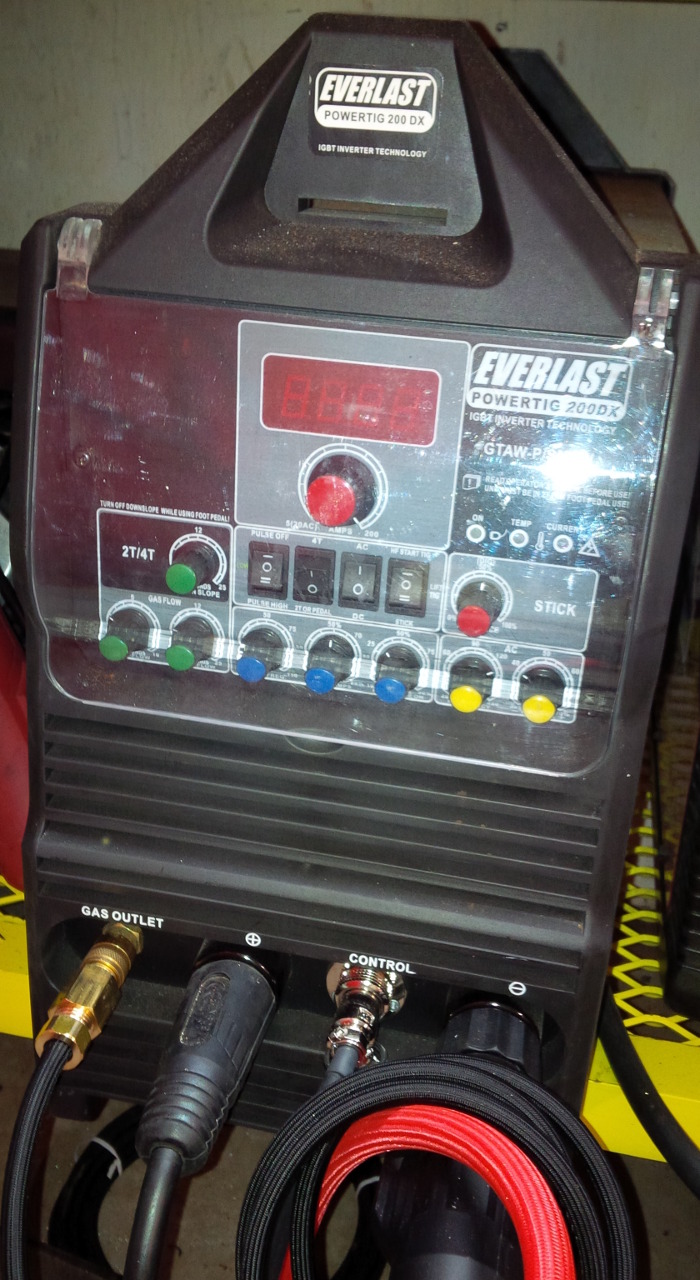
The welder itself is a great unit that has way more advanced features (pulse!) than you'd get from Red or Blue at this price point.
It is not without its flaws though:
The first is that the foot pedal it ships with is absolute junk. Mine died after only a few hours of use. Happily, there is a pro-level aftermarket replacement pedal from SSC Controls that fixes the problem permanently.
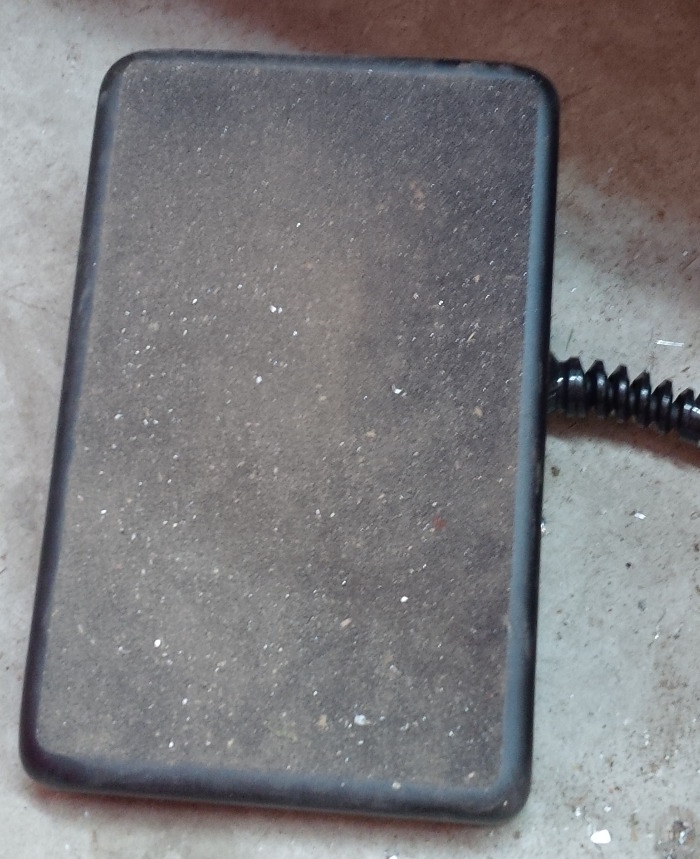
Secondly, the torch it comes with, while workable, is big, clumsy, and munches shielding gas. I was able to reduce gas consumption a little via a gas lens kit, but the real answer was to get a pair of good torches from CK. These torches are much lighter, the hoses are more flexible, and the clear gas lens nozzles let you see the arc better. I got a 130A torch and a 200A torch (links below). Note that they don't use the same DINSE adaptors!
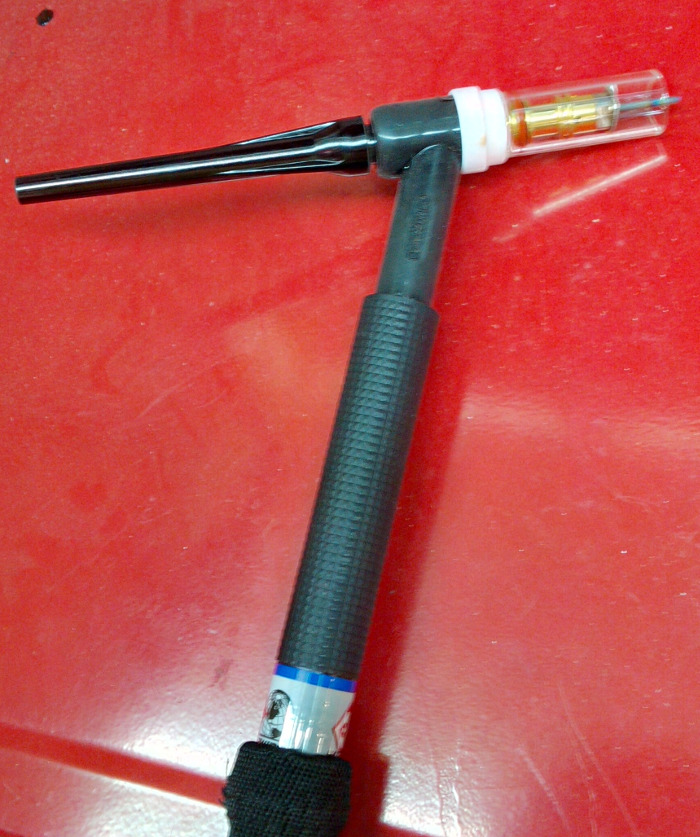
Also really handy is a TIG Finger prop support.
I wanted to provide flash protection for the shop and keep splatter and whatnot contained in the bay. So I picked up a custom curtain from strip-curtains.com and hung it from the roof.
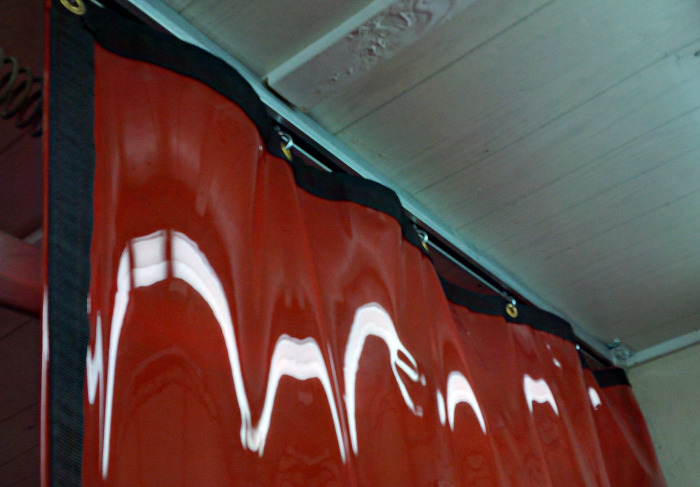
I wanted to be able to evacuate fumes - be they welding or otherwise - and this barn fan certainly does the trick.
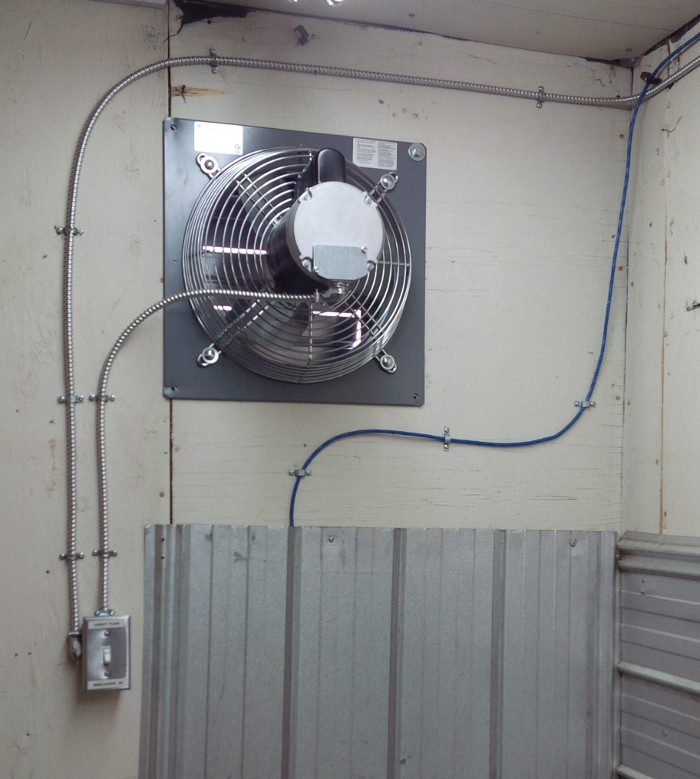
Now I just have to master the technique of welding aluminum....
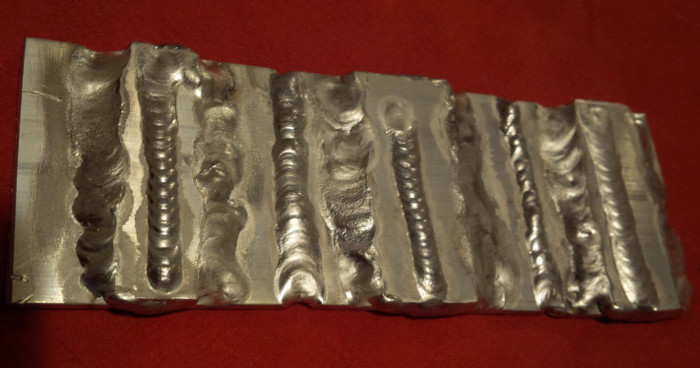